This is an original article, written by Ed Sowoski of Light Guide Systems.
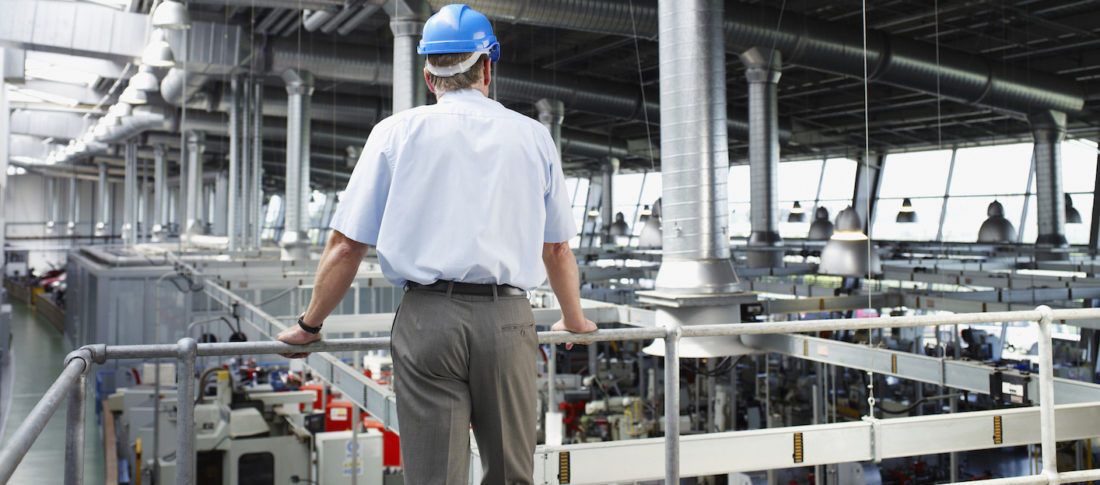
As a lean practitioner of many years, I have had the privilege of applying lean concepts in many different businesses including project engineering, repetitive manufacturing, process manufacturing and even in a sales capacity. I’ve had to apply lean principles in areas where the cycle times ranged from seconds to days, which allowed me to apply lean manufacturing tools in very different ways.
As a result, I have had the privilege of touring many plants from Large OEMs to Tier 2 and 3 “mom and pop” shops. As a passionate lean “zealot”, I took the time to learn about these companies’ lean practices and have been exposed to a lot of the common factors that cause organizations to excel (or struggle) with lean.
As I have benchmarked various organizations over the years, I’ve learned a tremendous amount about how to take the best lean principles from organizations operating in completely different industries and apply them in new, but similar, ways.
I have also heard of, and witnessed, horror stories about organizations that tried to apply benchmark best practices by attempting to “copy and paste” them into their organization, only to see it fail miserably. In those cases, the organization did not diligently observe the principles behind the system they were benchmarking. As a result, they missed key support elements and cultural aspects of the benchmark organization that made those best practices successful, neglecting to consider their own unique circumstances, culture and guiding principles.
As a young lean practitioner, I was taught the “tools” people use to improve processes, such as heijunka and kanban, were simply the best available countermeasure given the circumstance. For example, when kanban is utilized, single piece flow is often not an option due to the manufacturing process, so kanban is the best available countermeasure.
My point is, don’t get hung up on using kanban just for the sake of using kanban (i.e. “We’re a lean company, see we use kanban”), rather evaluate the problem, identify the waste and apply the best countermeasure you can find to solve that problem.
Enabling Creativity Before Capital and the Example of Karakuri
With that being said, simplicity and creativity before capital are core tenets of the thinking that is burned into the minds of lean practitioners, and rightly so. For instance, there are often much less expensive options available than automation. If you haven’t had a chance to learn about karakuri kaizen, watch this quick video introducing the topic:
At its core, karakuri is about making devices that move things using no external power sources, rather taking advantage of gravity, levers, pullies, etc. Karakuri is the essence of “creativity before capital” and continuous improvement because it requires iterative improvement, group problem solving and creativity.
While karakuri is a facet of lean thinking that is fascinating to me, I have found over the years that some lean practitioners have limited themselves and their organization by branding technology as evil. They don’t see the waste they’re creating by doing things manually when they could utilize technology for simple tasks that machines or computers do well, freeing up time and providing better data to improve team-based problem solving.
Another example of this can be seen in the error-proofing techniques that are used in lean manufacturing. If you search the terms mistake-proofing, error-proofing, or poke-yoke, you’ll find there is a massive amount of content available to help team members involved in manual operations reduce the errors made in manufacturing processes.
Yet despite great training programs and team member vigilance, humans are fallible and inevitably will make mistakes, such as forgetting to assemble a portion of a part, misassembling something, or improperly selecting or assembling the incorrect part. These are just a few of the common errors made in manual operations.
Enabling Technologies within the Lean Toolkit
This is a great example of where lean practitioners should not ignore the availability of technology as a viable countermeasure to continued quality issues where manual intervention exists.
A new technology has arisen, a countermeasure that can aid team members in avoiding common mistakes, helping reduce variation in training levels, improve knowledge of customer requirements and product knowledge, and eliminate the impact of common distractions that lead to errors. Furthermore, this countermeasure can eliminate the need to utilize other costlier and less-flexible error-proofing tools, such as templates, proximity sensors, and the like. What is it? Projection AR.
Projection AR as a Lean Manufacturing Tool
Projector-based AR platforms, like Light Guide Systems, provide team members with step-by-step guidance by projecting visual cues onto the part or work surface to aid them in correctly picking, packing, inspecting, assembling or training.
Because this relatively new countermeasure does not require the team member to wear a device to see the guidance, it creates a visual process that can be seen by the team member, their co-workers, as well as process auditors.
As is the goal with the 5S methodology, Light Guide Systems creates a visual process, bringing abnormalities to the surface immediately. With the help of a projected cycle time count down timer right in the team member’s field of view, for example, a team member or their team leader observing their work will know whether they’re on pace to complete their task in time or not. This can help lead to more timely and effective problem solving.
Simple human mistakes that are the result of distractions are eliminated because the guidance helps the operator know exactly where they are in the process. So, if a team member has to take a break, is distracted by their thoughts, or is stopped and asked a question, they will never make the mistake of missing a step. If they are distracted and accidentally reach to pick a similar part, the system gives them audible and visual feedback to grab their attention and ensure they pick and assemble the proper component.
The Light Guide Systems countermeasure not only ensures quality but also boosts productivity and, more importantly, harnesses the flexibility and intelligence of the team members in the process. Because there is no need for physical error-proofing devices or proximity sensors, a workstation or assembly line can become much more flexible, meeting the needs of customer demands for products with ever increasing customization and configurability.
Adding Augmented Reality to Your Lean Toolkit
A solution like Light Guide Systems is a practical countermeasure that lean and continuous improvement practitioners in every industry should be aware of and have in their tool belt.
Aside from the quality, productivity and training benefits, Light Guide Systems has two major benefits that are in line with the tenets of lean.
- Light Guide Systems helps reduce the stress and burden of worry that team members doing complex work carry. This is in line with one of the most important principles of “respect every individual” that we often discuss in lean circles.
- Reduced stress leads to a secondary benefit, as team members “mindwidth” is freed up to solve problems and come up with ideas for process improvement. Many other error-proofing devices take the team member out of the equation. Light Guide Systems uniquely harnesses the best of the human being, their heart and brain, while supplementing it with the help of technology.
Organizations that can tap into the intelligence and creativity of their team members are those who will beat their competitors, and Light Guide Systems is the modern day lean countermeasure that can help your organization do exactly that.
View the original article here.
To learn more about the IMEC approach to lean manufacturing and to set up a free lean assessment, contact us at 888-806-4632 or send an email to info@imec.org.